Universal Composite Submarine Camel. Groton, Connecticut.
Camels are utilized between a submarine and mooring structure to transfer berthing and mooring loads and provide necessary stand-off distances. Prior to the design and construction of the Universal Camel, the Navy had nearly twenty different camel designs constructed with traditional materials. The variety of existing designs and materials led to significant maintenance and replacement costs. For the new camels, fiber-reinforced polymer (FRP) sandwich panels were utilized as the primary structural element of the 36ft wide by 18ft tall camels. The prototype camel subsections were fabricated offsite and assembled at Submarine Base New London in Groton, CT. After flotation testing and final adjustments, the camels were put into service and have successfully berthed attack submarines.
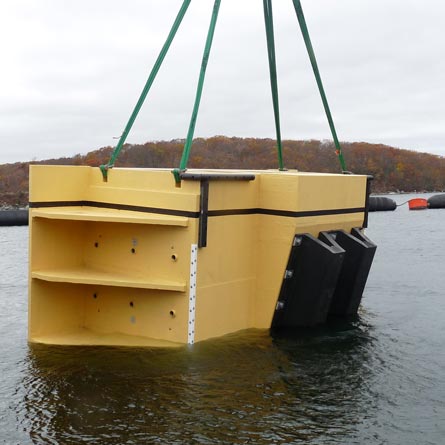
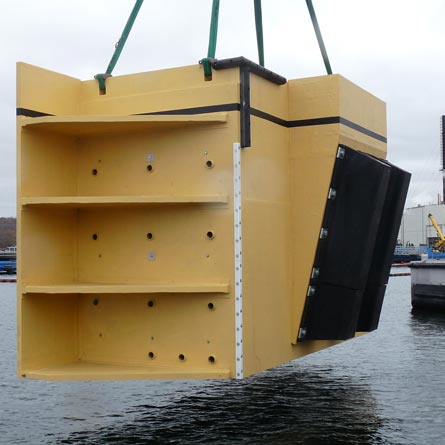
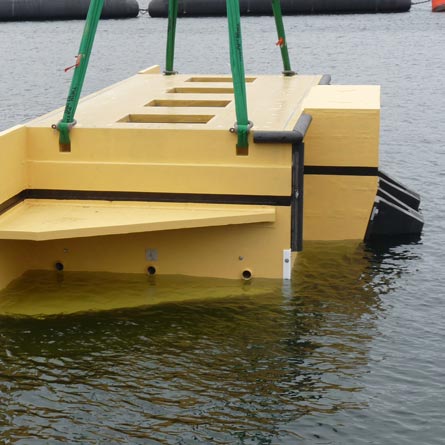
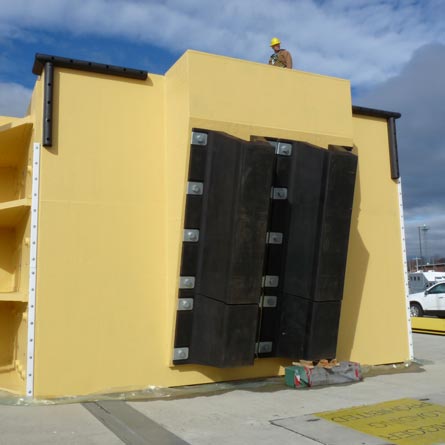
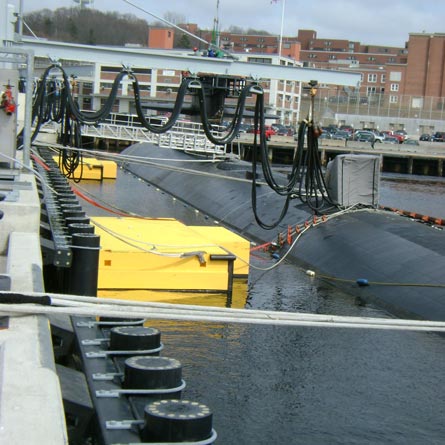
Services Performed
Project Highlights
Marine
WRA performed full berthing and mooring analysis of all active submarines currently in service with the U.S. Navy to determine the energy and reactions on the camels and camel support structure.
Structural
Structural design and analysis included design of the camel internal structure to resist reactions from submarine berthing analysis. Additional loading scenarios included lifting the camel into and out of the water, drag force on cleats when pulling the camel through the water, and connections of fenders and other elements.